The manufacturing process of medical infusion bags plays a crucial role in ensuring the safe and effective delivery of intravenous (IV) fluids and medications to patients. These bags are essential tools used in hospitals, clinics, and various medical settings. We will take you through the intricate process of how medical infusion bags are made by manufacturers.
Table of Contents
Introduction
Medical infusion bags are essential in delivering fluids and medications to patients. These bags are manufactured using high-quality materials and undergo strict quality control measures to ensure patient safety. The manufacturing process involves sterilization, resistance testing, and customization options. With different types of infusion bags available, including PVC and non-PVC options, medical professionals have a range of choices to meet their specific needs. From banana-shaped bags to IV saline bags, these bags are designed to be non-toxic and withstand thermal and compression forces. So, let’s dive into the comprehensive guide on how these infusion bags are manufactured.
What are Medical Infusion Bags?
Medical infusion bags are essential for delivering fluids, medications, and nutrients directly into a patient’s bloodstream. These bags are designed to be sterilized and made from materials like polyvinyl chloride (PVC), polypropylene (PP), polyethylene (PE), or TPE. These bags can withstand the pressure and maintain their integrity with good thermal and compression resistance. The manufacturing process involves strict quality control, ensuring the bags are non-toxic and have a hemolysis rate of hemolysis less than 5%. Medical infusion bags provide a reliable solution for safe and effective IV therapy.
Types of Medical Infusion Bags
Siny Medical infusion bags come in various types to cater to different medical needs. One common type is IV saline bags, which deliver fluids and medications directly into the bloodstream. These bags are typically made from high-quality materials and are sterilized to ensure safety.
Another type is TPE IV infusion bags, which are made from thermoplastic elastomers. These bags offer good resistance to thermal and compression forces, making them suitable for various medical applications.
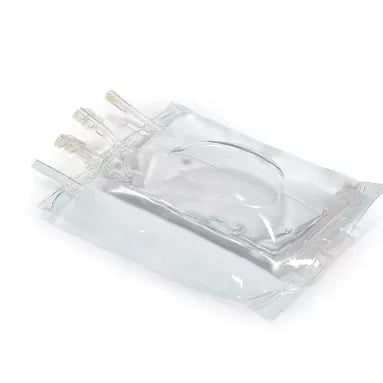
There are also non-PVC soft bag IV infusion bags, which are eco-friendly and non-toxic. These bags provide a safe and reliable option for intravenous infusions.
Medical professionals can choose the most appropriate option for their patient’s needs with different infusion bags available. From IV saline bags to TPE infusion bags, the medical industry has a variety of choices to ensure efficient and safe delivery of fluids and medications.
Materials Used
The primary materials used in the manufacturing of medical infusion bags are medical-grade plastics such as polyvinyl chloride (PVC) or polyethylene. These materials ensure the bags are safe for medical use.
Design and Planning
Manufacturers carefully plan the bag’s design, considering size, shape, and the number of chambers. The design must meet regulatory standards and user needs.
Extrusion of Plastic Films
Plastic films are extruded and cut into sheets of specific dimensions. These sheets will form the body of the infusion bag.
Printing and Labeling
Important information, including volume measurements, drug compatibility, and manufacturer details, is printed on the bags. Labels with barcodes are also attached for tracking.
Heat Sealing
The plastic sheets are heat-sealed to create the bag’s main compartments and channels for fluid flow. Precision is crucial to ensuring airtight seals.
Tube Attachment
Tubes for delivering fluids into and out of the bag are attached securely. This step requires precision to prevent leaks.
Materials Used in Manufacturing
Medical infusion bags are manufactured using various materials that meet industry standards. These materials undergo strict quality control to ensure the safety and functionality of the bags. One commonly used material is polyvinyl chloride (PVC), which provides good resistance to thermal and compression forces. Another material known for its eco-friendly qualities is polypropylene (PP).
Polyethylene (PE) and TPE (thermoplastic elastomer) are also used in manufacturing. These materials are sterilized using Ethylene Oxide (EO) to eliminate potential risks. The bags must support a certain amount of weight and have a low percentage of hemolysis.
Manufacturing Process
The manufacturing process of medical infusion bags involves several key steps. First, the materials, such as polyvinyl chloride (PVC), polypropylene (PP), polyethylene (PE), or medical-grade TPE, are selected based on their quality and suitability for the intended use. These materials are then thoroughly sterilized to ensure their safety.
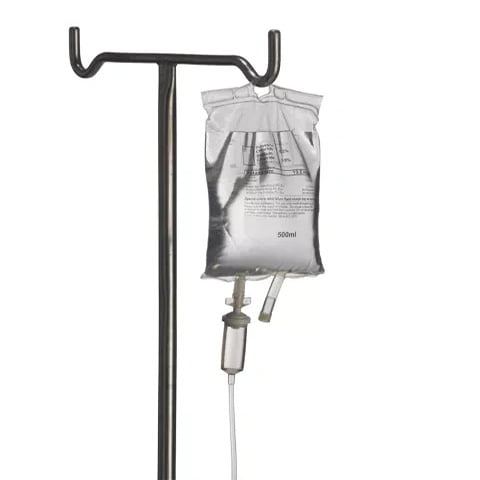
Next, the selected material is processed into the desired shape and size of the infusion bag. This is done through advanced manufacturing techniques, including blow molding or injection molding. The goal is to create a strong and durable bag that can withstand the pressure of the infusion process.
Once the bags are formed, they undergo strict quality control measures. This includes checking for bag defects or imperfections, such as leaks or weak spots. The bags are also tested for their resistance to thermal and compression forces, ensuring their reliability during use.
After passing the quality control tests, the bags are packaged and prepared for distribution. They are carefully sealed to maintain their sterility and prevent contamination.
The manufacturing process for medical infusion bags requires precision and attention to detail to ensure the highest quality and safety standards are met. By following strict protocols and utilizing advanced technologies, manufacturers can produce infusion bags that are reliable and suitable for medical use.
Quality Control in the Manufacturing of Medical Infusion Bags
During the manufacturing process of medical infusion bags, strict quality control measures are implemented to ensure the safety and effectiveness of the final product. These measures include:
Raw Material Testing: The raw materials used in the production of medical infusion bags, such as PVC, PP, and PE, undergo rigorous testing to ensure they meet the required quality standards. This helps to prevent any contamination or defects in the final product.
Production Line Inspections: Regular inspections are carried out on the production line to ensure that all manufacturing processes are followed correctly. This includes checking for any deviations or abnormalities that could affect the quality of the infusion bags.
Sterilization Validation: Infusion bags must be sterilized to eliminate potential pathogens or microorganisms. Sterilization validation tests are conducted to verify the effectiveness of the sterilization process and ensure that the bags are free from any harmful contaminants.
Leakage and Strength Testing: Infusion bags undergo rigorous testing to check for leaks or weaknesses. This involves subjecting the bags to various stress tests, including applying pressure and simulating transportation conditions, to ensure they can withstand their intended user’s demands.
Implementing these stringent quality control measures, manufacturers can ensure that medical infusion bags meet the highest safety and reliability standards, providing healthcare professionals with a reliable tool for delivering fluids and medications to patients.
Conclusion
In conclusion, medical infusion bags are essential to the healthcare industry. They come in various types, including PVC, PP, PE, and TPE bags. These bags are manufactured using high-quality, eco-friendly materials and undergo strict quality control measures to ensure their safety and effectiveness.
The manufacturing process involves sterilization by EO and testing for resistance to thermal and compression forces. The bags must meet certain criteria, such as supporting 60 minutes under 15 N force and having a low percentage of hemolysis.
Medical infusion bags are critical in delivering fluids and medications to patients. Their quality and design make them reliable and safe in healthcare settings.
Now that you comprehensively understand how medical infusion bags are manufactured, you can appreciate the complexity and precision behind these crucial medical devices. So, the next time you see an infusion bag, remember the meticulous process it went through to ensure the well-being of patients.
Faq Infusion Bags
What is an infusion bag?
An infusion bag, also known as an IV (intravenous) bag, is a sterile and flexible container designed to hold medical fluids, such as saline solutions, medications, blood products, or nutrients. These bags are integral to healthcare and are used to administer fluids and medications directly into a patient’s bloodstream through an intravenous line.
What is the use of an infusion bag?
An infusion bag’s primary benefit is delivering fluids, medications, or other therapeutic solutions intravenously to patients. Healthcare professionals use infusion bags to maintain a patient’s hydration, provide essential nutrients, administer medications, and perform various medical treatments. Infusion bags are crucial in hospitals, clinics, and other healthcare settings to ensure accurate and controlled delivery of fluids and medications.
What materials are infusion bags made of?
Infusion bags are typically made from medical-grade plastics. Common materials include polyvinyl chloride (PVC) and polyethylene. These plastics are chosen for their compatibility with medical use, flexibility, and ability to maintain the sterility of the contents. Some advanced infusion bags may be made from more environmentally friendly materials as part of sustainability efforts in healthcare.
How are infusion bags made?
The manufacturing process of infusion bags involves several steps:
- Extrusion of Plastic Films: Medical-grade plastic is extruded and cut into sheets of specific dimensions, forming the body of the infusion bag.
- Printing and Labeling: Important information such as volume measurements, drug compatibility, and manufacturer details are printed on the bags. Labels with barcodes for tracking may also be attached.
- Heat Sealing: The plastic sheets are heat-sealed to create the bag’s main compartments and channels for fluid flow. Precise sealing is essential to prevent leaks.
- Tube Attachment: Tubes for delivering fluids into and out of the bag are securely attached. This step requires precision to ensure airtight connections.
- Quality Control: Stringent quality control measures are in place to check for defects and ensure each bag meets safety standards.
- Sterilization: The bags undergo sterilization to eliminate potential contaminants and maintain sterility until use.
- Packaging: Sterile bags are packaged in clean and secure environments to prevent contamination before reaching medical facilities.
Infusion bags are manufactured with utmost precision and attention to detail to ensure they meet the high standards required for medical use, safeguarding patient health and safety.